SOLEX IMPELLER TECHNOLOGY
Industrial process engineering agitation is a unit operation that involves the random distribution of a substance in different phases to achieve a desired process result. Fluid mixing plays a major role in processing a multitude of products and with the correctly selected equipment it is possible to mix, combine, suspend or disperse any liquid, slurry or gas. Sol-Mix designs and manufactures agitation and mixing systems catering for light, medium and heavy duty applications.
These applications may range from simple slurry storage in open tanks to complex chemical reaction systems under extreme conditions of temperature and pressure.
Medium to heavy duty agitators are used predominantly in the mining, mineral processing, chemical, sewage and water treatment industries. While the light duty range is predominately used in the food and pharmaceutical industries.
Correct impeller choice will minimise absorbed power without compromising the mixing efficiencies for the particular application. Therefore, every impeller selection is custom designed to optimise the cost and performance associated with a particular application.
Sol-Mix offers a range of impeller systems from high efficiency hydro-foil impellers to pitched, flat or curved blade turbines. Customised mixer and agitator system design is possible by combining any of the above mentioned impeller types to achieve the required mixer duty.
The robust design and construction of the Sol-Mix agitator minimises maintenance requirements and extends service life. The Sol-Mix agitator is designed for optimum mechanical strength which enables it to transmit the full gearbox output torque while withstanding the cyclic forces associated with mixing.
Any successful agitator design must provide some required level of process performance. Although process performance has many meanings in the chemical process industries, agitator design has been quantified for most typical applications. Our mixing design procedure is one of the best methods for relating agitation intensity to process performance.
Our team of highly trained engineers will design an optimal mixing solution for your specific mixing requirement. Using a fluid mixing design software to simulate the performance of your existing agitator system, we can recommend a superior agitator design that will optimize your mixing by reducing batch time and power consumption and improving product quality. Under the brand name of "Sol-mix" We supplies a wide range of mixing systems to the Pharmaceutical, Agrochemical, Specialty Chemicals, Biotech, Paints, Paper & Pulp industries. We design and manufacture mixing systems for various
Applications:
- Blending/Heat Transfer
- Suspension
- Emulsification
- High Viscosity Blending
- Gas Dispersion
Advantages:
- Reduction in Power Consumption without compromising the mixing requirement
- Improvement in mixing performance like Heat Transfer and Mass Transfer
- Blending or Solid Suspension, Blend time
- Small and Compact systems
- Easy Maintenance.
What is mixing?
Mixing as a concept is about reducing inhomogeneity. It can be inhomogeneity in concentration, phase or temperature. This might seem like a simple problem to solve, but is really a complex process involving theories of fluid mechanics and a large amount of know-how. In the industry mixing is needed in paper pulp manufacturing, sewage disposal, oil manufacturing, manufacturing of chemicals and in many other processes.
The media mixed can vary a lot and so can the goal of the mixing process. In chemical industries the mixing is often about getting a homogeneous fluid in shortest time possible while in some of the process steps of sewage disposal the mixing is applied in order to avoid stagnation and the stirring has to be as economical as possible i.e. lowest possible power ensuring the proper mixing. There are numerous terms describing the nature of the mixing process, shown in below table.
The table below describes possible combinations of media to be mixed and the goals of the mixing process in terms accepted and used in the industry.
Most of these terms are more thoroughly described later and it will be shown how important Scanpump's know how is to achieve the goals of the different processes, considering the choice of vessel, impellers and other tools (e.g. motors, gear boxes, etc.) used in the process.
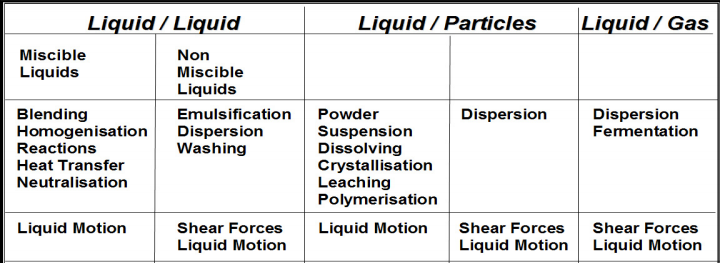
Types of Flow in Agitated Tank
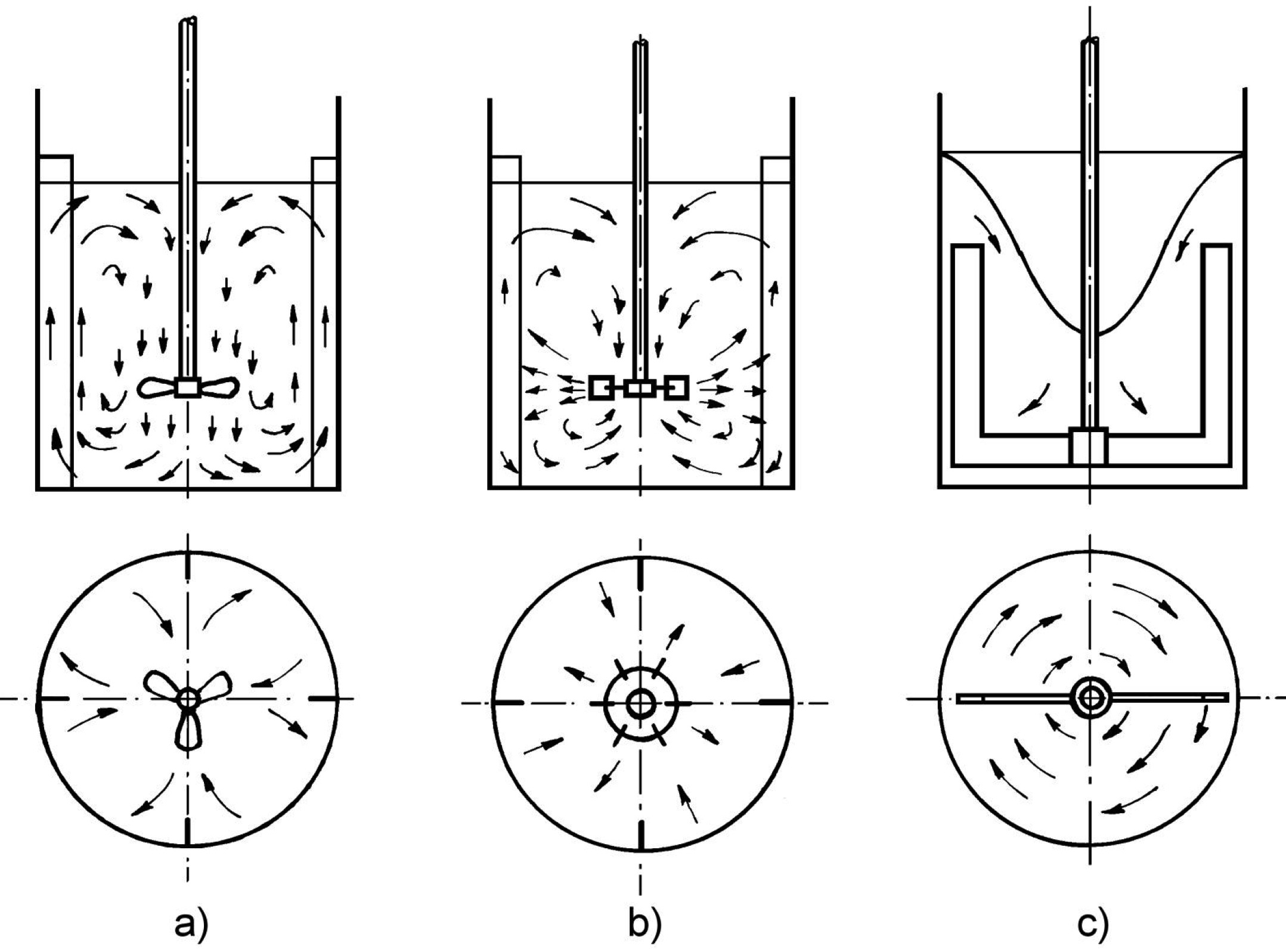
- a) Axial-flow pattern, baffled vessel
- b) Radial-flow pattern, baffled vessel,
- c) Tangential-flow pattern, unbaffled vessel
Mainly 4 Factors for Configuring Your Fluid Mixer
CONSIDERING MIXER CONFIGURATION
If you’re in an industry that includes fluid mixing in its processes, you probably know that finding the right fluid mixer for your needs is critical to maintaining quality control, reducing costs, and optimizing efficiency.
The key here is to engineer a fluid mixer that addresses the specific needs of your process. When configuring a mixer for your process, your mixing engineer should consider the following 4 factors:
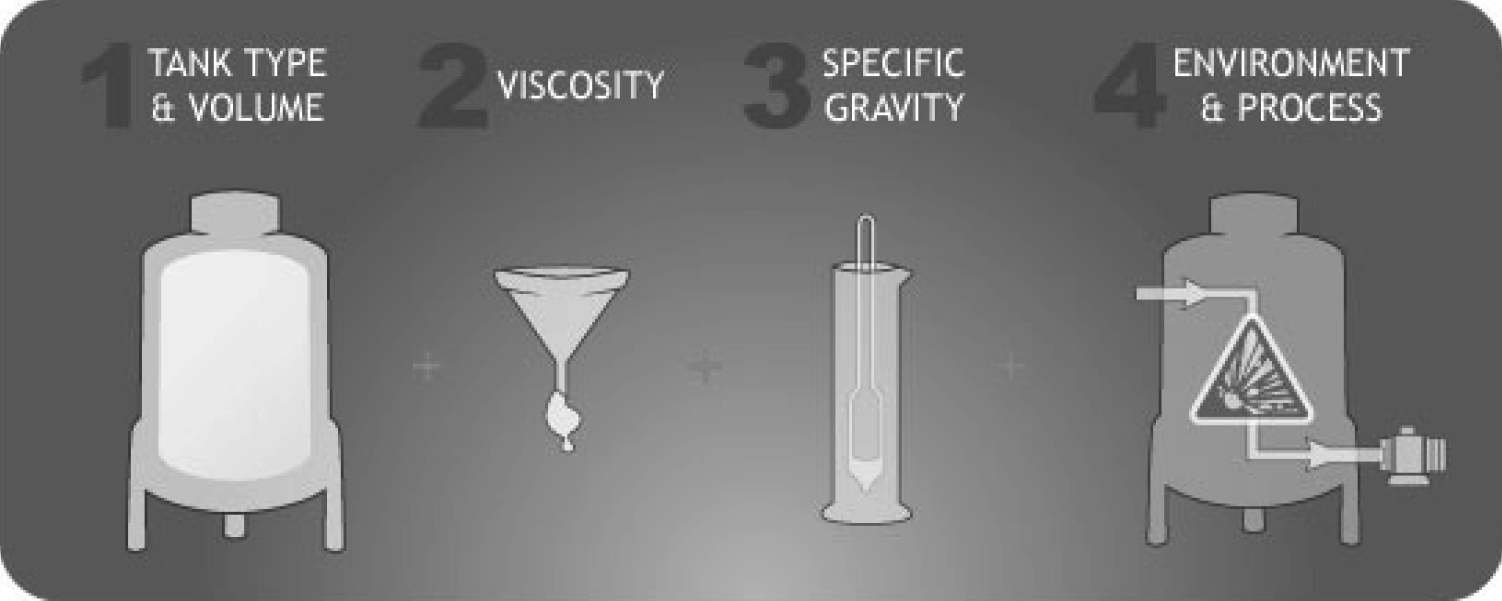
Factor #1 – Tank Type & Volume
This determines the amount of fluid your tank can hold. This is important because it will determine the size and position of the fluid mixer and its mounting.
Factor #2 – Viscosity
This is “thickness” or “internal friction” of your fluid. It’s important because it will determine the impeller and horse power configurations.
Factor #3 – Specific Gravity
This is the density of the solid in comparison to water. It’s important because it will determine the type of pumping action that is required to adequately mix your fluid.
Factor #4 – Environment & Process
This is the setting where your mixing will take place. It’s important because it can determine the type of power source and finishes.
With this information in hand, our mixing engineer should configure a mixer with the following qualities:
- 1. Motor with suitable horse power and energy source
- 2. Gear drive optimized for torque capacity
- 3. Mounting fitted according to your tank needs
- 4. Impeller sized to maximize efficiency
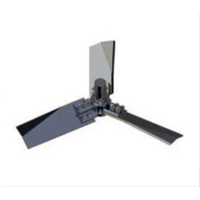
HIGH EFFICIENCY IMPELLER
An established industry standard for axial flow impellers
Extremely efficient creates greater fluid motion with less energy
Ideal for blending, heat transfer and solids suspension
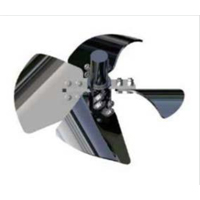
TRANSITION FLOW TURBINE
Excellent performer in abrasive solids suspension , liquid-solid-gas and boiling applications
High-solidity blade design translates into higher gas rates and viscosity values over other high efficiency designs
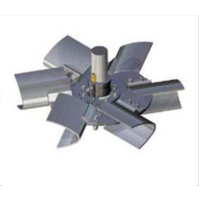
GAS DISPERSION TURBINE
Advanced design
Highest gas dispersing capability at near ly six times the D-6 (Rushton) turbine
Reduced unloading
Relatively insensitive to viscosity
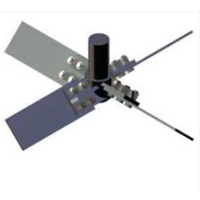
PITCHED BLADE TURBINE
Aril flow design suitable for wide changes in process viscosity
Good for blending and solids suspension where elevated shear is needed
Able to handle higher gas rates over high efficiency designs
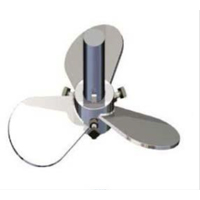
PROPELLER
Marine style energy efficient design
Ideal for small batches
Handles higher viscosities than hydrofoil designs
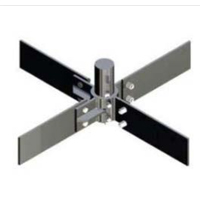
STRAIGHT BLADE TURBINE
Close clearance design for operation near the tank bottom
Excellent for low-liquid足 level solids suspension applications
Designed for use in laminar regime (Reynolds number < 50) applications
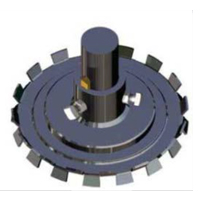
COWL DISC
Customize levels of shear to suit your process
Proper fluid turnover minimizes the need for auxiliary pumping impellers
Small particles possible : 2 microns achieved in processes such as micro足 encapsulation
Traditiona l dispersion blades can also be used in high shear applications
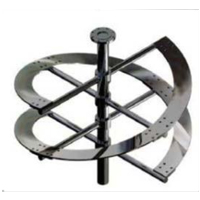
DOUBLE HELICAL RIBBON
Proven the best high viscosity, laminar flow impeller
Highly effective in heat transfer
Efficiently incorporates surface liquids and solids
For viscosities over 30,000 Mpa
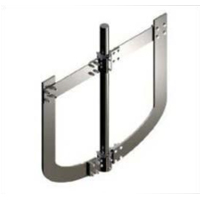
ANCHOR
Most economical laminar flow impeller available
Horizontal flow well suited for low-liquid足level geometries
Solve heat transfer fouling problems with optional wall scrapers
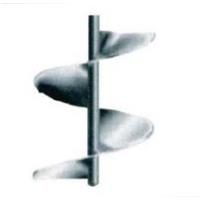
SCREW
Ideal for shear sensitive, uniform blending applications (polymers)
Excellent top-to足bottom turnover flow characteristics
Use in mildly pseudoplastic applications with power law indexes as low as 0.5